Vibration Analysis 101: Essential Guide to Understanding Vibration Monitoring
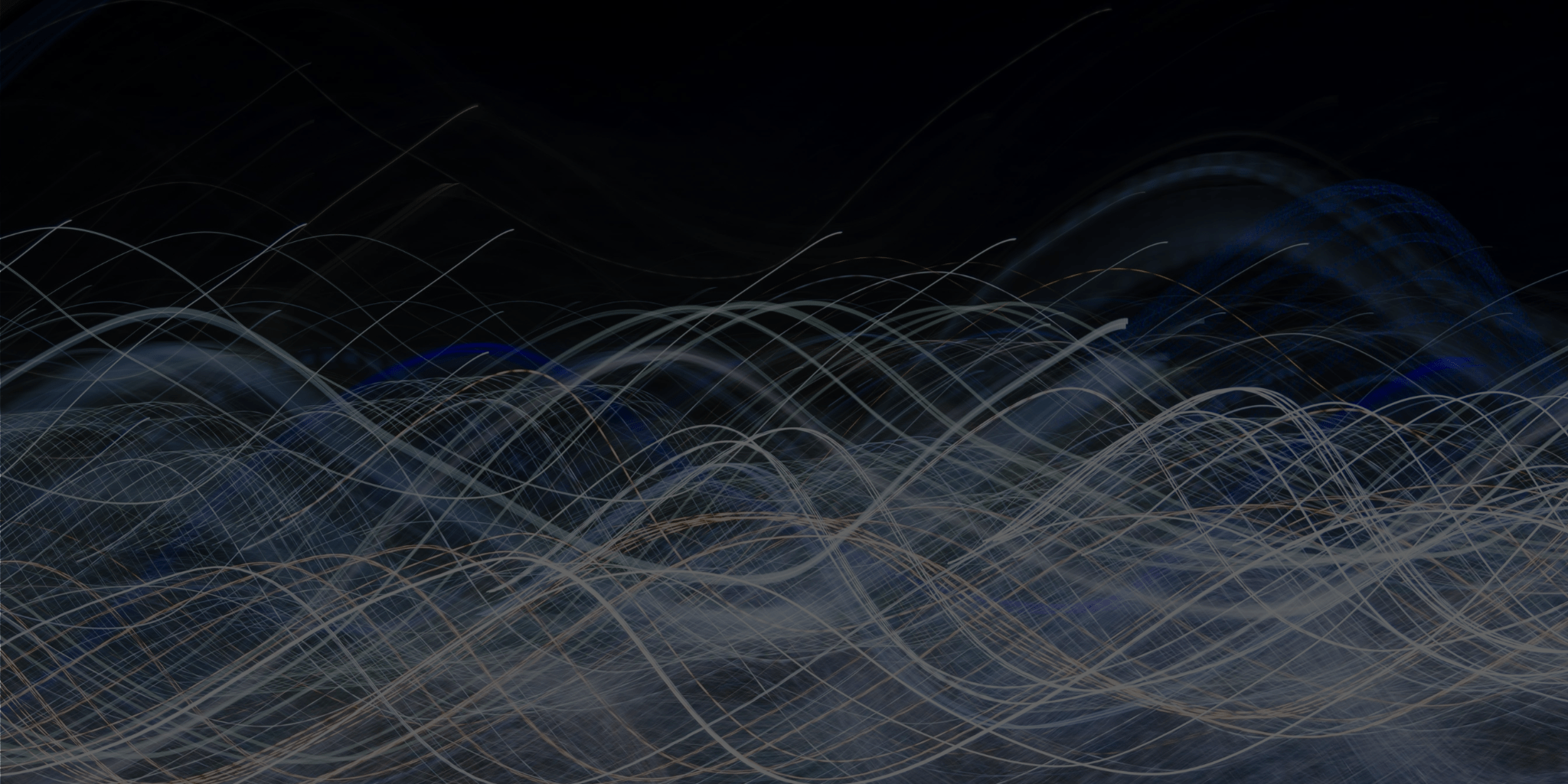
Every piece of rotating equipment in your facility is constantly communicating with you. Motors, pumps, fans, compressors, and turbines all send out signals through vibration patterns that reveal their operational health, efficiency, and potential problems. The question is: are you listening?
Vibration monitoring has emerged as one of the most powerful predictive maintenance (PdM) tools available to modern industry, offering the ability to detect equipment issues weeks or months before catastrophic failure occurs. This comprehensive guide will walk you through everything you need to know about vibration monitoring, from basic concepts to implementation strategies.
What is Vibration Monitoring?
It’s all about the numbers.
Vibration monitoring is the process of measuring and analyzing the oscillatory motion of machinery components to assess their condition and performance. When equipment operates, it naturally produces vibrations due to rotating parts, mechanical forces, and various operational dynamics. These vibrations create unique signatures that change predictably as equipment degrades or develops faults.
Think of vibration monitoring as taking the pulse of your machinery. Similar to a doctor detecting health issues by monitoring changes in your heartbeat, maintenance professionals can identify equipment problems by tracking changes in vibration patterns over time.
WAITES INSIGHT
At Waites, we treat vibration data like a health report. Our analysts interpret these signals every day, often identifying faults that internal teams missed with handhelds or visual inspection.
Why Vibration Monitoring Matters
The financial impact of unexpected equipment failure extends far beyond repair costs. Unplanned downtime can cost manufacturers anywhere from $50,000 to more than $500,000 per hour, depending on the industry and scale of operations. Vibration monitoring addresses this challenge by enabling a proactive maintenance approach that delivers significant benefits.
- Cost reduction is one of the most substantial and immediate benefits. By identifying issues early, organizations can schedule repairs during planned maintenance windows, avoiding expensive emergency repairs and overtime labor costs. The ability to order parts in advance rather than expediting them can significantly reduce procurement and logistics costs.
- Extended equipment life occurs when problems are caught and corrected before they cause secondary damage. A simple bearing replacement caught early might cost a few hundred dollars. However, equipment failure in later stages could potentially result in costly delays to replace a specialized or high-demand asset, leading to downtime.
- Improved safety becomes critical when considering that rotating equipment failures can pose serious risks to personnel. Vibration monitoring helps prevent catastrophic failures that could result in flying debris, hot oil spills, or other dangerous situations.
- Enhanced productivity results from more reliable equipment operation and reduced unplanned downtime. When maintenance teams can predict when equipment will need attention, production schedules become more predictable and efficient.
Understanding Vibration Fundamentals
To effectively implement vibration monitoring, it's essential to understand the basic physics involved. Vibration is characterized by several key parameters that provide insight into equipment condition. Here are the four primary terms you need to understand.
Frequency (Data) |
Spectrum (Display) |
Amplitude (Data) |
Waveform (Display) |
Common Vibration Problems and Their Signatures
Understanding the relationship between specific equipment problems and their vibration signatures is crucial for effective monitoring. Each type of mechanical issue creates distinct patterns that trained analysts can recognize and interpret.
- Imbalance is indicated by high vibration at running speed. This issue occurs when the mass center of a rotating component doesn't align with its geometric center, creating a centrifugal force that produces strong vibrations at exactly the running frequency of the equipment. Imbalance typically shows up as high radial vibrations with consistent phase relationships across the machine.
- Misalignment happens when coupled shafts don't share the same centerline. Angular misalignment creates vibrations at twice the running frequency (50% or more of the primary frequency), while parallel misalignment produces axial vibrations at the running frequency. The combination of these patterns, along with high temperatures at coupling locations, typically indicates misalignment.
- Bearing defects generate complex vibration patterns related to the bearing's internal geometry. Rolling element bearings produce vibrations at specific frequencies calculated from the bearing dimensions, number of rolling elements, and operating speed. These frequencies are typically much higher than running speed and often appear with associated harmonics and sidebands. Some bearing defect reasons include improper installation, inadequate lubrication, operating conditions such as misalignment and imbalance, and adverse environments (e.g. external vibration, contaminants).
- Structural looseness occurs when the machine is not correctly supported to its base, typically at running speed. It may produce a one-time signal in the radial direction predominant in the horizontal reading. Measurements should be made on the bolts, feet, and bases to determine a change in the amplitude and phase. A decrease in amplitude and 180-degree phase difference will confirm this problem. Additionally, rotating looseness occurs by an excessive clearance between the rotor and the bearing.
- Resonance occurs when operating frequencies coincide with natural frequencies of machine structures. This amplifies vibration levels and can lead to rapid equipment degradation. Resonance problems often appear suddenly following changes in operating speed or structural modifications.
PRO TIP
Waites analysts often diagnose bearing issues triggered by poor lubrication or external vibration. These subtle causes are easily missed without expert eyes.
Additional common failure modes include bent shaft, gear wear, cracked or broken gear teeth, chain wear and looseness, cavitation, rolling element bearing defects, tilt pad bearing wear, loose bearing mounts, resonance, belt wear and looseness, sheave run-out, fluid and airflow problems, oil whirl and whip, and many electrical problems.
Vibration Measurement Techniques
Effective vibration monitoring requires proper measurement techniques and equipment selection. The choice of sensors, measurement locations, and data collection methods significantly impacts the quality and usefulness of vibration data.
- Accelerometers are the most common vibration sensors, converting mechanical motion into electrical signals proportional to acceleration. These sensors offer wide frequency response, good sensitivity, and robust construction suitable for industrial environments. Piezoelectric accelerometers provide excellent high-frequency response, while MEMS accelerometers offer cost-effective solutions for less demanding applications.
- Velocity sensors measure vibration velocity directly and are particularly sensitive to mid-frequency problems common in rotating machinery. These sensors often integrate accelerometer signals electronically to provide velocity output, combining the benefits of solid-state construction with velocity measurement advantages.
- Proximity probes measure shaft displacement directly by detecting changes in the distance between the probe tip and shaft surface. These sensors are essential for monitoring large rotating machinery like turbines and compressors, where shaft motion relative to bearing housings provides critical information about equipment condition.
- Measurement locations must be carefully selected to ensure vibration data accurately represents equipment condition. Generally, measurements should be taken at bearing locations in three perpendicular directions: horizontal, vertical, and axial. The sensor should be mounted as close as possible to the bearing, with a solid mechanical connection to ensure accurate signal transmission.
Data Analysis and Interpretation
Raw vibration data becomes valuable information only through proper analysis and interpretation. Modern vibration analysis combines time-domain and frequency-domain techniques to extract maximum insight from collected data.
- Time waveform analysis examines vibration signals as they vary over time, revealing information about impacts, intermittent problems, and signal modulation. Time waveforms are particularly useful for identifying bearing defects, gear problems, and looseness issues that create characteristic patterns in the time domain.
- Frequency analysis transforms time-domain signals into frequency-domain spectra using Fast Fourier transform (FFT) algorithms. Frequency spectra reveal the individual frequency components within complex vibration signals, making it possible to identify specific problems based on their characteristic frequencies.
- Trending analysis tracks how vibration parameters change over time, which provides insight into equipment degradation rates and remaining useful life. Effective trending requires consistent measurement conditions and locations. If a location changes from one reading to the next, trends will become inaccurate. In some cases, even moving the sensor location half an inch will have a tremendous impact on the trend.
- Advanced techniques include envelope analysis for bearing diagnostics; phase analysis for alignment and balance problems; and order analysis for variable-speed equipment. These specialized techniques provide additional diagnostic capability for complex problems that may not be apparent in basic vibration spectra. Phase analysis is important for helping technicians locate the components that are involved with looseness issues.
Building a Vibration Monitoring Program
Successful vibration monitoring requires a systematic approach that addresses technology, procedures, and personnel development. A well-designed program balances cost-effectiveness with diagnostic capability while fitting seamlessly into existing maintenance workflows.
- Program planning begins with identifying critical equipment and establishing monitoring objectives. Not all equipment requires the same level of monitoring; resources should be focused on machines where failure would have the greatest impact on safety, production, or costs. Risk-based selection criteria help prioritize equipment and determine appropriate monitoring intervals.
- Route development organizes measurement locations and sequences to optimize data collection efficiency. Effective routes consider equipment criticality, accessibility, safety requirements, and logical geographic sequences. Route design should also account for equipment operating conditions and environmental factors that might affect measurement quality.
- Personnel training is essential for program success. Technicians need training in proper measurement techniques, safety procedures, and basic data interpretation. Analysts require more advanced training in vibration theory, diagnostic techniques, and software operation. Ongoing education ensures personnel stay current with evolving technology and best practices.
- Technology selection involves choosing appropriate sensors, data collectors, and analysis software based on equipment types, monitoring objectives, and available resources. Portable data collectors offer a flexible, cost-effective option for route-based monitoring, while online systems provide continuous data collection for critical assets. Wireless systems offer the best of both, enabling continuous coverage without the labor of manual routes and freeing up in-house technicians to focus on machines that show signs of change and require deeper or more advanced testing.
REAL-TIME WINS
Waites' cellular gateways and wireless nodes enable real-time alerts and analyst intervention, no IT integration needed.
Best Practices for Success
Implementing vibration monitoring successfully requires attention to numerous details that can make the difference between a program that provides valuable insights and one that generates data without corresponding benefits.
- Consistent procedures ensure data quality and enable meaningful comparisons over time. Standardized measurement locations, sensor mounting methods, and measurement parameters reduce variability that could mask developing problems or create false alarms.
- Quality control processes should verify data accuracy and identify potential measurement problems. Regular calibration of instruments, verification of measurement locations, and review of unusual readings help maintain data integrity.
- Documentation standards enable knowledge transfer and ensure continuity as personnel change. Comprehensive documentation should include equipment information, measurement procedures, baseline data, and historical problem patterns.
- Continuous improvement involves regularly reviewing program effectiveness and adjusting procedures based on experience and changing requirements. Feedback from maintenance personnel, equipment reliability data, and cost-benefit analysis help optimize program performance.
Vibration Monitoring Continues to Evolve
Vibration monitoring technology is evolving rapidly, driven by advances in sensor technology, wireless communication, artificial intelligence, and cloud computing. These developments promise to make vibration monitoring more accessible, accurate, and valuable.
Artificial intelligence (AI) and machine learning (ML) are automating pattern recognition and diagnostic processes that previously required experienced analysts. These technologies can process large amounts of data, identify subtle patterns, and provide diagnostic recommendations with increasing accuracy.
IoT integration enables vibration sensors to become part of broader industrial internet ecosystems, sharing data with other monitoring systems and enterprise applications. This connectivity facilitates more comprehensive asset management and predictive maintenance strategies.
Edge computing allows more sophisticated analysis to be performed locally at the sensor level, reducing data transmission requirements while enabling faster response to developing problems.
Getting Started with Vibration Monitoring
For organizations beginning their vibration monitoring journey, success depends on starting with realistic objectives and building capability systematically.
Begin by identifying a small number of critical machines and establishing basic monitoring procedures. Focus on gaining experience and demonstrating value before expanding the program scope.
Consider partnering with experienced consultants or service providers like Waites to accelerate learning and avoid common pitfalls. Many equipment manufacturers and condition monitoring specialists offer training programs and consulting services that can help establish effective monitoring practices.
Remember that vibration monitoring is ultimately about making better maintenance decisions. The technology and techniques are simply tools for gathering and interpreting information that enables more proactive, cost-effective equipment management.
START SMART WITH WAITES
We help clients move from pilot to plant-wide coverage without retraining, re-integrating, or re-spending. Immediate results. Long-term reliability.
Transform Maintenance. Reduce OPEX. Operate Reliably.
Vibration monitoring represents one of the most mature and effective predictive maintenance technologies available today.
When properly implemented, it provides early warning of equipment problems, enables optimized maintenance scheduling, and delivers substantial returns on investment through reduced downtime and maintenance/operational costs.
Success requires understanding both the technical aspects of vibration measurement and analysis, as well as the organizational elements necessary to integrate monitoring data into maintenance decision-making processes. With proper planning, training, and implementation, vibration monitoring can transform equipment maintenance from a reactive, crisis-driven activity into a proactive, data-driven discipline that supports improved reliability, safety, and profitability.
The investment in vibration monitoring technology and training pays dividends through more reliable equipment operation and the confidence that comes from truly understanding the health of your critical assets.