Predictive Maintenance
Today’s modern, fast-paced industrial operations require uptime all the time. Companies understand maximizing asset availability, increasing operational efficiency, and driving down maintenance costs are more important than ever.
That’s why predictive maintenance (PdM) is now table stakes, foundational to every plant manager’s reliability strategy. Advancing real-time data analytics and empowering faster decision making, PdM is a no-brainer. When combined with the latest artificial intelligence (AI) and machine learning (ML) tools, it can pick up where traditional time-based preventive maintenance strategies drop off: detecting the invisible to avoid costly unplanned downtime.
Our PdM experts have put together a comprehensive guide covering the ins and outs of predictive maintenance. Examine how it works, the different types and key technologies involved, and measurable benefits for multiple industries.
Enter the Virtual Situation Room
Picture this: your phone buzzes with an alert. It's the reliable team you depend on day and night to monitor your most critical equipment. One of Rob’s go-to vibration analysts from Waites is informing you that Pump #3 is showing early signs of wear and will need attention in about two weeks.
No panic. No emergency shutdowns. Just a proactive heads-up from your AI-powered Waites sensor and the certified vibration expert behind it, focused on resolving issues before they escalate, so you can sleep easier knowing there’s always a watchful eye on the ground.
Welcome to our vision of creating a world where nothing breaks™. Where factories of the future are enhancing productivity with predictive intelligence tools that help mitigate anomalies before they escalate into expensive, potentially catastrophic, failures. These AI-powered solutions help scale PdM efficiently and cost-effectively across dispersed sites and thousands of assets, without added complexity or concern.
So, where do you start with PdM, and how does it improve situational awareness? It begins with understanding the core components that make this solution essential for modern operations.
What Is Predictive Maintenance?
Predictive maintenance is a proactive asset management approach that monitors the condition and performance of equipment in real time to predict when maintenance should be performed. The goal is to conduct maintenance at the right time—not too early, which wastes resources, and not too late, which can lead to catastrophic equipment failure.
PdM is a cornerstone of modern reliability-centered maintenance (RCM) strategies and is foundational to the Industrial Internet of Things (IIoT), Industry 4.0, and smart manufacturing initiatives. Unlike reactive maintenance (repair after failure) and preventive maintenance (scheduled servicing), PdM uses data to forecast equipment failure and optimize maintenance schedules. The core principle involves continuous monitoring of equipment health indicators, statistical analysis of degradation patterns, and probabilistic modeling of failure progression.
PdM systems typically integrate multiple condition monitoring technologies to provide comprehensive asset health assessment, including vibration analysis, thermography, oil analysis, electrical signature analysis, and increasingly, computer vision-based visual intelligence systems.
Why Predictive Maintenance Matters
Predictive maintenance enables organizations to make informed decisions about equipment servicing and replacement based on actual machine condition rather than fixed schedules or gut instinct. This results in significant improvements across key operational metrics:
- Reduced downtime: Identify issues early and plan repairs proactively.
- Lower maintenance costs: Eliminate unnecessary preventive maintenance and minimize emergency repairs.
- Extended equipment lifespan: Prevent minor issues from escalating into major damage.
- Improved safety: Reduce the risk of hazardous failures in critical systems.
- Higher productivity: Ensure more consistent asset performance and fewer operational disruptions.
These outcomes have made predictive maintenance a necessity in sectors such as manufacturing, logistics, oil and gas, food and beverage, mining, and utilities. PdM represents one of the most practical and proven pathways to digital transformation.
Its impact is grounded in data and field experience, and its success lies in its foundation: a deep, empirical understanding of how industrial assets behave over time and under stress.
Built on Proven Foundations
Predictive maintenance focuses on the assets that matter most: pumps, motors, compressors, and other critical rotating equipment. These machines have been monitored for decades, giving the industry a deep, field-tested understanding of how they fail and how to catch problems early. Modern PdM platforms apply that accumulated knowledge at scale, with today's tools built on years of real-world experience that enables faster diagnosis, fewer surprises, and a more proactive maintenance approach.
Low-Risk, High-Impact Implementation
Unlike many transformation efforts, PdM doesn't disrupt operations. Most systems collect data while equipment runs normally, allowing teams to improve performance and reduce downtime without interrupting production. This makes it a low-risk, high-impact investment and, for many industrial teams, the smartest place to start their digital transformation journey.
How Predictive Maintenance Works
01. Data Collection
Predictive maintenance starts with collecting operational data from machinery and equipment. PdM typically uses a range of sensors that measure key performance indicators such as:
- Vibration (to detect imbalance, misalignment, or wear)
- Temperature (to identify overheating or friction)
- Pressure and flow (in hydraulic or fluid systems)
- Electrical current (for motors and pumps)
- Acoustic emissions and ultrasonic signatures
Sensors are either embedded in equipment or retrofitted as part of a condition monitoring system. The data is then transmitted to a central repository for processing, often in real time.
02. Data Transmission
Sensor data is transmitted via wired connections or wireless technologies such as Bluetooth, Wi-Fi, or dedicated mesh networks. In modern PdM systems, data is sent to cloud-based platforms for storage and analysis. Edge computing processes data locally when low latency is vital.
03. Data Analysis and Modeling
Once collected in the cloud or edge processing unit, data is analyzed using:
- Machine learning algorithms: These identify patterns, trends, and anomalies based on historical and real-time data.
- Statistical models: Regression and time-series models help forecast failure probabilities and estimate remaining useful life (RUL).
- Rule-based systems: Trigger alerts based on predefined thresholds.
04. Condition Assessment and Prognostics
After analysis, the system generates insights that maintenance teams can act on. These include:
- Predictive alerts (e.g., "Bearing X will fail within 12 days")
- Recommendations for part replacement or inspection
- Visual dashboards showing real-time machine health
Advanced PdM systems integrate with Computerized Maintenance Management Systems (CMMS) to automatically generate work orders and streamline maintenance scheduling.
05. Decision and Action
Maintenance and reliability teams use these insights to prioritize and plan interventions. This helps align maintenance schedules with production cycles, minimizing disruption.
With greater focus on reducing unplanned downtime and supporting consistent asset performance, PdM strategies help maximize production output—ultimately driving greater operational efficiency and increased revenue.
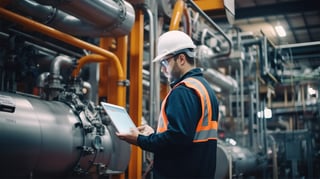
Predictive Maintenance ROI in Action: Inside The Numbers That Matter
EVERY MINUTE OF DOWNTIME IS A DIRECT HIT TO PRODUCTIVITY, PROFITABILITY, AND REPUTATION
Waites changes the ROI equation. Delivering ROI in just 3 to 6 months—often faster. This isn’t a future-state scenario. It’s happening now, in real plants, with measurable impact. Let’s break down how.
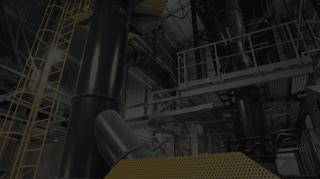
OWENS CORNING PREVENTED AN $11 MILLION LOSS WITH THE WAITES PREDICTIVE MAINTENANCE SOLUTION
Discover how a global leader in construction materials transformed its maintenance strategy with Waites' AI-driven solution - averting a single catastrophic breakdown that could have cost over $11 million.
How Predictive Maintenance Works in Practice
Modern PdM platforms are built on decades of real-world experience. Their diagnostics and alerting strategies reflect more than 50 years of hands-on troubleshooting, across motors, pumps, compressors, and conveyors. This depth of knowledge enables teams to move faster and adopt with confidence.
PdM operates in the background while equipment is running, collecting the right data and transforming it into actionable insights that help you stay ahead of failure, without pausing production or changing workflows.
Types of Predictive Maintenance Technologies
Several technologies support predictive maintenance. Often, a combination of methods is used for comprehensive coverage.
Vibration Analysis
- Detects mechanical faults like imbalance, misalignment, and bearing defects.
- Suitable for rotating equipment such as motors, fans, and compressors.
- The most mature PdM technology, vibration analysis, provides comprehensive fault detection for rotating machinery. ISO 20816 standards define measurement procedures and evaluation criteria. Advanced techniques include:
-
Envelope Analysis: High-frequency demodulation for bearing fault detection.
-
Order Tracking: Speed-compensated analysis for variable-speed machinery.
- Operational Deflection Shapes (ODS): Modal analysis for structural resonance issues.
- Bump Testing: Impact-response analysis for looseness and structural integrity.
-
Thermal Imaging
- Identifies hot spots in electrical panels, motors, and bearings.
- Common in high-voltage and power distribution systems.
- Infrared thermography detects thermal anomalies with high spatial resolution. ASNT TC-1A certification ensures technician competency. Applications include:
- Electrical Systems: Hot spots in switchgear, transformers, and motor connections.
- Mechanical Systems: Bearing overheating, belt misalignment, and coupling problems.
- Process Equipment: Heat exchanger fouling, refractory damage, and insulation
Ultrasonic Testing
- Detects high-frequency noise from leaks, electrical arcing, and friction.
- Useful in compressed air systems, steam traps, and lubrication checks.
- Ultrasonic condition monitoring detects high-frequency acoustic emissions from:
- Mechanical Sources: Bearing lubrication issues, cavitation, and turbulence
- Electrical Sources: Partial discharge, arcing, and corona discharge
- Leakage Detection: Compressed air, steam, and hydraulic system leaks
Oil Analysis
- Evaluates oil quality and contamination levels in gearboxes, engines, and turbines.
- Predicts wear and helps optimize lubrication schedules.
- Comprehensive tribological monitoring includes:
- Wear Metal Analysis: ICP spectroscopy for elemental detection down to 1 ppm.
- Particle Counting: Laser-based systems per ISO 4406 cleanliness standards.
- Additive Analysis: Remaining useful life of lubricant packages.
- Contamination Detection: Water content, fuel dilution, and solid particle ingression.
Electrical Signature Analysis
- Monitors motor current and voltage to detect winding and insulation faults.
- Motor current signature analysis (MCSA) and power quality monitoring detect:
- Rotor Defects: Broken rotor bars and end ring cracks through slip frequency analysis.
- Stator Faults: Winding asymmetry and turn-to-turn faults.
- Mechanical Issues: Eccentricity, misalignment, and load variations
- Power Quality: Voltage unbalance, harmonic distortion, and phase imbalance.
Infrared Spectroscopy and Acoustic Emissions
- Advanced methods for detecting subtle degradation in materials or systems.
Benefits of Predictive Maintenance
01. Cost Savings
Predictive maintenance significantly reduces maintenance expenses by preventing unnecessary repairs and minimizing expensive emergency work. According to industry studies, PdM can reduce maintenance costs by up to 30% and decrease breakdowns by over 70%.
02. Increased Uptime and Reliability
By catching failures early, organizations experience fewer disruptions and avoid the domino effect of unexpected downtime. This is especially critical for continuous production lines and just-in-time manufacturing environments.
03. Better Asset Utilization
PdM maximizes the value of equipment by extending its operational life and ensuring that machinery operates at optimal performance levels.
04. Improved Workforce Efficiency
Maintenance teams shift from reactive fire-fighting to strategic, data-driven interventions. This reduces stress, improves planning, and helps manage staffing challenges.
05. Enhanced Safety and Compliance
Well-maintained equipment poses fewer safety risks and is more likely to meet regulatory requirements, especially in industries with stringent operational standards.
06. Scalability and Flexibility
Modern PdM systems are modular and scalable, making it possible to implement them in small facilities and scale up to multi-site enterprises without overhauling existing systems.
07. Peace of Mind
When equipment health is continuously monitored (removing guesswork) and potential issues are flagged early, there’s less concern for emergency breakdowns and more confidence in asset conditions. PdM sensors provide peace of mind with 24/7 equipment surveillance, allowing engineers to focus on strategic improvements during regular hours rather than responding to crises at all hours.
08. Data-driven Decision Making
Advanced PdM analytics unlock additional improvements in root cause analysis, maintenance strategy optimization, capital planning and benchmarking.
Challenges & Implementation Considerations
While predictive maintenance offers clear benefits, successful implementation requires attention to key challenges:
- Initial Investment: Upfront costs for sensors, software, and integration can be significant.
- Data Quality and Quantity: Effective prediction relies on clean, sufficient, and high-resolution data.
- Organizational Buy-In: Resistance to change from traditional maintenance practices can slow adoption.
- Cybersecurity: Connected systems must be protected against data breaches and unauthorized access.
- Training and Skills: Teams need training in new tools and interpretation of predictive analytics.
Overcoming these hurdles requires a strategic approach, including pilot projects, stakeholder engagement, and phased rollouts.
Real-World Applications of Predictive Maintenance
- Manufacturing: In discrete and process manufacturing, PdM is used to monitor CNC machines, conveyor systems, robotics, and hydraulic presses. By reducing downtime, manufacturers improve throughput and maintain tight delivery schedules.
- Oil and Gas (Petrochemical): PdM is critical for offshore platforms and refineries where equipment failure can have catastrophic consequences. Sensors monitor pumps, valves, and compressors to ensure continuous production and safety.
- Automotive and Aerospace: Predictive analytics ensure high reliability for mission-critical systems, from assembly lines to aircraft engines. Condition monitoring enhances quality assurance and reduces warranty claims.
- Utilities and Energy: PdM supports grid stability by monitoring transformers, generators, and wind turbines. It enables efficient load balancing and minimizes blackout risks.
- Food and Beverage: In F&B environments, PdM helps ensure compliance with hygiene standards while avoiding contamination and spoilage due to machine failure.
The Future of Predictive Maintenance
Predictive maintenance continues to evolve with advancements in AI, edge computing, and digital twins. Trends shaping the future include:
- Self-learning algorithms that adapt to each asset's unique operating conditions.
- Edge AI for faster, localized analysis and reduced cloud dependency.
- Digital twins that simulate equipment behavior and enable scenario-based planning.
- Predictive maintenance-as-a-service (PdMaaS) platforms that offer plug-and-play solutions for SMEs.
- Integration with ERP and MES Systems to streamline maintenance and production planning.
As these innovations mature, predictive maintenance will become more accessible, automated, and accurate.
Getting Started with Predictive Maintenance
Organizations looking to adopt predictive maintenance should consider the following steps:
- Assess current maintenance practices: Identify high-impact assets and common failure modes.
- Start small: Launch a pilot project with a subset of critical equipment.
- Choose the right technology: Select sensors and software tailored to your assets and budget.
- Establish data infrastructure: Ensure reliable data collection, transmission, and storage.
- Build internal expertise: Train staff or partner with experts to interpret insights and act accordingly.
- Measure success: Track KPIs like downtime reduction, cost savings, and RUL accuracy.
- Scale strategically: Expand across facilities and asset classes as value is demonstrated.
Reduce Uncertainty. Boost Confidence.
Every plant manager strives for safe, reliable, efficient, and compliant operations at all times. That means operating with zero defects and downtime whenever and as often as possible.
Predictive maintenance is no longer a futuristic concept—it’s a proven strategy that enables companies to transition from reactive to proactive asset management. PdM sensor technology paired with actionable intelligence pinpoints equipment issues with greater accuracy and speed. Modernizing maintenance with sensors improves asset reliability and predictability, increases safety, and lowers opex.
By harnessing real-time data, advanced analytics, and intelligent insights, PdM also empowers organizations to drive operational excellence.
Manufacturers that embrace automation and AI-powered industrial solutions will experience greater uptime and stay competitive with this value-added technology.
Whether you’re just starting your journey or looking to refine an existing program, embracing predictive maintenance is an investment in resilience, efficiency, and competitive advantage.
Ready to take the next step with Waites? Schedule a meeting with us to start scaling predictive maintenance across your industrial operations or check out our complete solution overview.
Looking to learn how Waites helps industrial teams scale predictive maintenance across complex operations? Check out our complete solution overview.
Frequently Asked Questions About Predictive Maintenance
What types of equipment benefit most from predictive maintenance?
PdM is especially valuable for critical, high-value assets like pumps, motors, compressors, conveyors, and turbines—any equipment where failure would cause significant downtime or safety risks.
How is predictive maintenance different from preventive maintenance?
Preventive maintenance follows a fixed schedule, while predictive maintenance uses real-time data to service equipment only when needed, reducing unnecessary work and costs.
What data is needed for predictive maintenance?
Common data sources include vibration, temperature, pressure, electrical signals, and acoustic emissions, collected via sensors and analyzed using advanced algorithms.
What are the biggest challenges in implementing PdM?
Upfront investment, data quality, change management, and cybersecurity are common hurdles. Starting with a pilot project and partnering with experienced vendors can help overcome these challenges.
How quickly can we see ROI from predictive maintenance?
Many organizations see measurable reductions in downtime and maintenance costs within the first year of implementation, especially when focusing on high-impact assets.
Say Hello
Discover our company, the stories of our customers and partnerships,
and schedule a meeting with Waites experts for reliability at every piece
of movable equipment at your production plant.