How Predictive Maintenance Helps You Do More with Less in a Labor-Constrained Industry
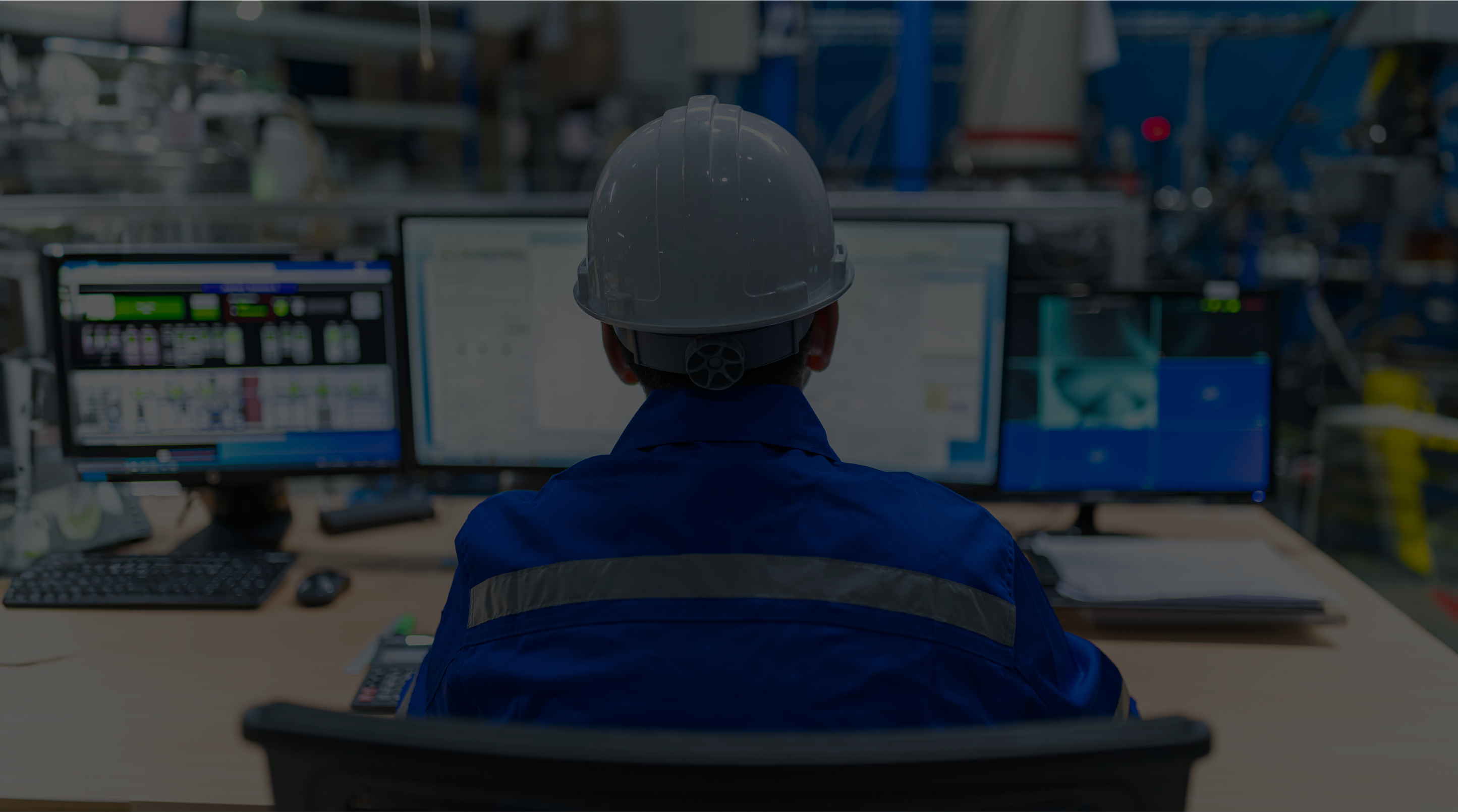
While U.S. manufacturing is poised for high growth and profitability fueled by smart technology investment and reshoring efforts, the sector faces a persistent challenge: a skills and applicant shortage across industries. Approximately 3.8 million manufacturing jobs will likely be needed by 2033, according to research from Deloitte and the Manufacturing Institute. Adding to this conundrum, manufacturers will require higher-level skills as they continue their journey toward Industry 4.0.
Enter predictive maintenance (PdM), a technology-driven approach that transforms how lean organizations can manage their most critical assets. Rather than waiting for equipment to fail or adhering to rigid preventive schedules, PdM puts sensors, data analytics, and machine learning to work to anticipate problems before they occur. The result is a maintenance strategy that maximizes asset uptime while minimizing the human resources required to achieve it.
PdM represents a fundamental shift in how businesses can thrive despite current workforce constraints. Companies already implementing this approach are reporting significant reductions in unplanned downtime and maintenance costs with leaner teams that can focus on strategic, high-value activities rather than emergency repairs.
For small to mid-size organizations scaling for the future, PdM offers a competitive advantage—doing more with less without the trade offs. In today’s constrained labor market, adapting your maintenance strategy with smart monitoring solutions will bridge this divide.
Scaling Knowledge Through Smart Technology
As more baby boomers and Gen X workers retire, their operational wisdom also exits the field. Intelligent tools help capture tribal knowledge and critical systems expertise to help maintain productivity and uptime during this transition. In many cases, this knowledge doesn’t have to come from inside the facility. Third party vibration analysis can monitor equipment health, flag emerging issues, and support teams as an extra set of expert eyes, without adding internal headcount. Offsite PdM specialists working remotely to monitor equipment health not only can apply actionable insights to predict and prevent downtime but also to onboard new talent as an extension of the operations team.
In today’s mobile, modern industrial environments, workers can now automate repetitive tasks while accessing more data than ever before.
As a cost-effective and efficient way to scale knowledge through technology, PdM builds on decades of human expertise. It brings forward better and more timely data to detect and prevent equipment problems as early as possible while also leveraging historic data to avoid disruptions and major overhauls.
The vibration patterns that a veteran technician learned to recognize over 20 years can now be captured by sensors and analyzed by algorithms trained on that same expertise. The thermal signatures that once required an experienced eye are now automatically detected and flagged by smart monitoring systems.
Rather than replacing human intuition with cold technology, PdM amplifies and democratizes the knowledge that master technicians possess.
The algorithms not only detect anomalies, but they also encode the decision-making patterns of these specialists, creating a scalable framework for equipment diagnosis that can guide less experienced team members.
Workforce Enablement in Action
Modern PdM systems serve as force multipliers for maintenance teams operating with constrained resources. A junior technician equipped with predictive insights can prioritize work orders with the confidence that comes from decades of institutional knowledge. Instead of learning through trial and error—or worse, through costly equipment failures—new hires can immediately tap into the collective wisdom of the organization.
The technology creates structured pathways for skill development. Predictive alerts identify problems as well as explain the underlying conditions, recommended actions, and potential consequences. This context transforms routine maintenance calls into learning opportunities, helping technicians understand what to fix and why it’s needed—and how to prevent similar issues in the future.
Consider a scenario where vibration analysis detects early-stage bearing degradation in a critical pump. A traditional approach might involve sending an experienced technician to investigate, diagnose, and plan the repair. With modern PdM, the system identifies the failure mode, recommends the intervention timeline, and guides a less experienced technician through the process. The senior technician becomes a consultant rather than the sole executor, multiplying their impact across multiple sites or systems. And when that senior-level expertise isn’t available in-house, third party analysts can help fill the gap, guiding newer techs through diagnosis and resolution, so that nothing slips through the cracks.
Accelerated Expertise Development
Today's maintenance professionals are developing expertise faster than previous generations, thanks to the structured learning environment that PdM creates. Where it once took years to learn the subtle signs of impending equipment failure, modern technicians can now access pattern recognition capabilities from day one.
PdM’s data-rich environment creates a feedback loop that expedites the learning process and preserves this knowledge for future reference. Technicians can see the progression of equipment degradation over time, understand the relationship between operating conditions and failure modes, and build their diagnostic skills through guided experience rather than pure trial and error.
This acceleration is crucial in addressing the skilled labor shortage. Organizations can't afford the traditional 5-10 year learning curve for developing master technicians. PdM compresses this timeline by providing immediate access to expert-level insights while still allowing individuals to develop their own intuitive understanding of equipment behavior.
Building Capabilities, Not Just Preventing Failures
The most significant impact of predictive maintenance may not be in the downtime it prevents, but in the capabilities it builds.
PdM doesn't just protect machines. It enhances human decision-making.
By providing structured access to diagnostic insights, recommended actions, and outcome tracking, PdM creates a continuous learning environment. Technicians develop broader expertise faster, gain confidence in their abilities, and can take on more complex challenges sooner in their careers.
This workforce development effect compounds over time. As more technicians develop advanced skills quicker, the organization builds deeper bench strength and resilience. The knowledge base expands rather than contracts, even as experienced personnel retire.
The Multiplication Effect
In a labor-constrained environment, the key to doing more with less is multiplying the effectiveness of existing resources. PdM achieves this multiplication by:
- Extending expertise across geographic boundaries
A single expert can guide maintenance decisions across multiple facilities through centralized monitoring and remote diagnostics. - Optimizing resource allocation
Predictive insights help teams focus their limited time on the highest-priority issues, reducing reactive work and emergency repairs. - Creating self-reinforcing learning cycles
Each maintenance action informed by predictive data contributes to the organization's knowledge base, making future decisions more accurate and efficient. - Enabling proactive capacity planning
Understanding equipment degradation patterns helps organizations plan workforce deployment and skill development more strategically.
PdM Leads the Way
The industrial maintenance sector will continue to face labor constraints for the foreseeable future. Organizations that view predictive maintenance purely as a technology investment miss its greatest value proposition: the ability to scale human expertise and accelerate workforce development.
The most successful implementations treat PdM as a knowledge management system that leverages sensors and algorithms. They focus not only on detecting equipment problems, but also on building organizational capabilities that can adapt and grow over time.
In this context, PdM becomes more than a maintenance strategy. It is a powerful workforce development platform that helps organizations preserve institutional knowledge, drive experiential learning, and build the expertise needed to thrive in an increasingly complex industrial environment.