Is Your Vibration Analysis Program Maturing—Or Just Aging?
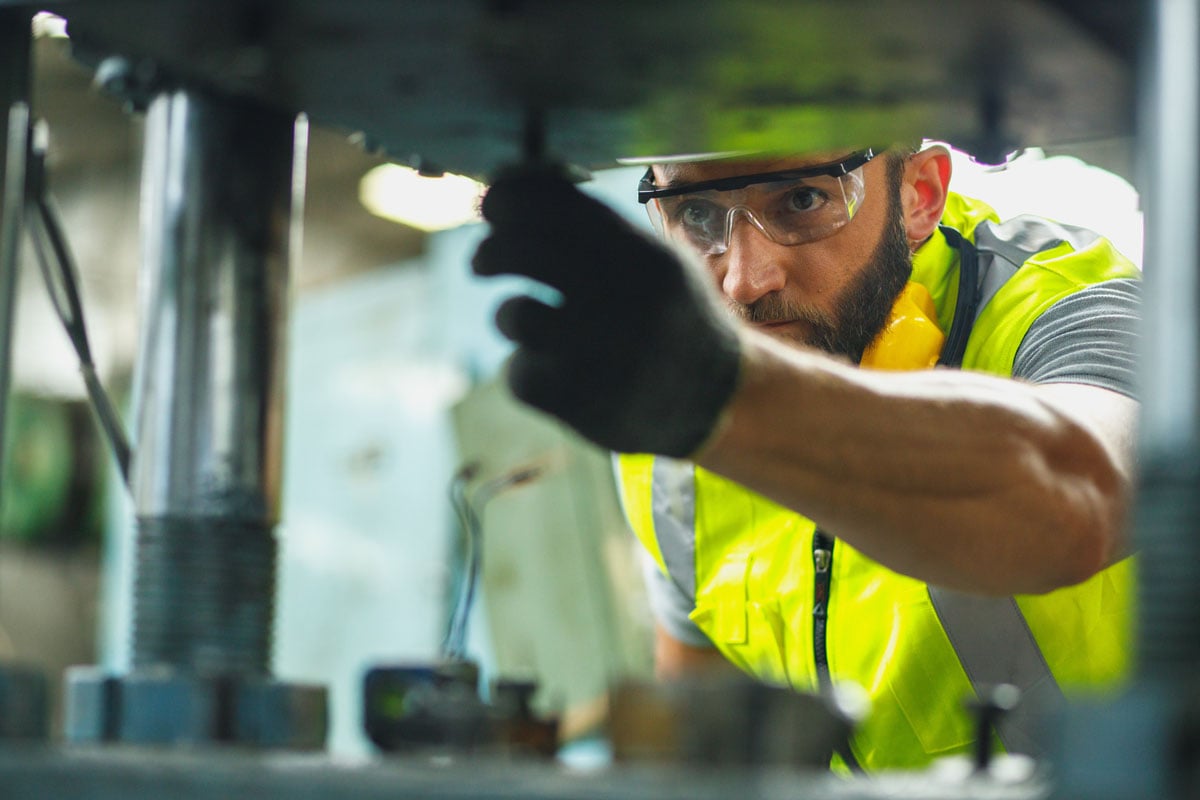
Not all vibration analysis programs are created equal. Some are built to grow, adapt, and improve over time. Others? They plateau—relying on outdated tools and inefficient routines while teams are stretched thinner than ever.
The question is simple, but critical: Is your vibration program keeping pace with what your operation really needs?
At Waites, we believe a truly maturing program isn’t just about more data—it’s about smarter decisions, greater coverage, and making your human resources count where they matter most.
From Data Collector to Strategic Contributor
For years, vibration technicians walked miles of routes, collecting data from hundreds of machines every month. And they didn’t just capture numbers—they used their eyes, ears, and instincts to spot early warning signs. Pipe leaks. Structural issues. Misalignments. A loose bearing might show up in a waveform, but a sharp ear or a burned smell might be the first red flag.
As tools evolved—better resolution, tri-axial sensors, real-time alarms—technicians could monitor more assets in less time. But the core model stayed the same: manual collection, manual review, reactive follow-up.
With wireless condition monitoring, that model is finally being rewritten.
What Changed—And Why It Matters Now More Than Ever
Since 2020, the manufacturing and industrial world has experienced a seismic shift. COVID accelerated retirements. Contractor availability dropped. Spare parts became harder to source. Skilled maintenance talent became scarce—and expensive.
And in this climate, doing “more with less” became the new reality.
That’s where wireless vibration monitoring, powered by real-time data and AI, isn’t just a “nice-to-have.” It’s the foundation of modern reliability. And it changes everything.
What a Maturing Program Looks Like Today
Here’s what sets a maturing vibration analysis program apart:
- Online, always-on wireless sensors collect data multiple times per day—no more waiting for routes.
- AI and machine learning screen for meaningful changes, so your analysts focus only where it matters.
- Fewer manual tasks means technicians have time for value-driving work like precision alignments and root cause analysis.
- Follow-up verification is instant—no waiting for machines to run or teams to be dispatched.
- Facility-wide coverage expands with fewer headcount requirements.
This isn’t automation for the sake of efficiency. It’s automation that amplifies human expertise and protects uptime.
It’s Not About Replacing People. It’s About Redeploying Them.
Let’s say you free up 40 to 60 hours per month by replacing manual routes with wireless sensors. That doesn’t mean your tech’s job disappears. It means they can now:
- Respond faster to true equipment issues.
- Spend time on alignment, balancing, and other precision tasks.
- Train new personnel and support other PdM initiatives (ultrasound, oil analysis, thermal imaging).
- Investigate deeper trends flagged by AI, not just run standard reviews.
Meanwhile, AVO (audio, and visual, and olfactory) inspections that used to happen during routes can be reassigned to trained operators or junior techs—keeping coverage wide without burning out your most experienced personnel.
Real-World Impact: What Wireless Condition Monitoring Delivers
- Faster QA Post-Maintenance
What once took hours—loading a route, walking out, collecting data, dumping and analyzing—is now a real-time check that takes 15 minutes tops. You'll have immediate confidence that your repair worked. - Better Coverage for Hard-to-Access Equipment
Conveyors that only run at night. Pumps that only run with certain loads. These used to be challenges—now they’re opportunities for better insights without schedule juggling or overtime. - Catching Transient Events
Vibration that spikes under specific environmental or load conditions is often missed in route-based collection. Online systems catch it, timestamp it, and correlate it with process changes. - Layered Diagnostics
When wireless sensors are tied to flow, pressure, or temperature data, root cause analysis becomes faster and more precise. You’re not just reacting—you’re diagnosing with clarity.
From Hours Saved to Value Delivered
A technician who no longer walks routes every day doesn’t disappear from your org chart. Instead, they become the engine behind:
- Increased wrench time
- Improved alignment and balancing outcomes
- Faster issue resolution
- Reduced downtime and emergency call-outs
- Deeper institutional knowledge sharing
This is how condition monitoring scales—not by replacing people, but by enabling the right people to do the right work.
Final Thoughts: Evolution Starts with a Decision
If you're still relying solely on manual routes, the question isn’t whether your vibration analysis program is outdated. It’s whether your team is being allowed to operate at its highest potential.
A wireless condition monitoring system won’t replace your people—it will make them more powerful. AI won’t eliminate your analysts—it will elevate their insight.
Start where it matters most: critical assets, hard-to-reach machines, or areas where contractor support is limited. From there, build a program that grows with you.
Mark Kingkade
Reliability Solutions Architect, Waites Sensor Technologies
Ready to Mature Your Program?
Let’s talk about where your vibration analysis program stands today—and where it could be with a wireless, AI-powered foundation that scales with your needs. Because great technology is only as valuable as the team behind it.