After analysts confirmed bearing wear from rising high-frequency trends, the maintenance team proactively scheduled a replacement during planned downtime to avoid production loss.
CASE STUDY Targeted Motor Bearing Monitoring Prevents Extensive Downtime in Tire Manufacturing Facility
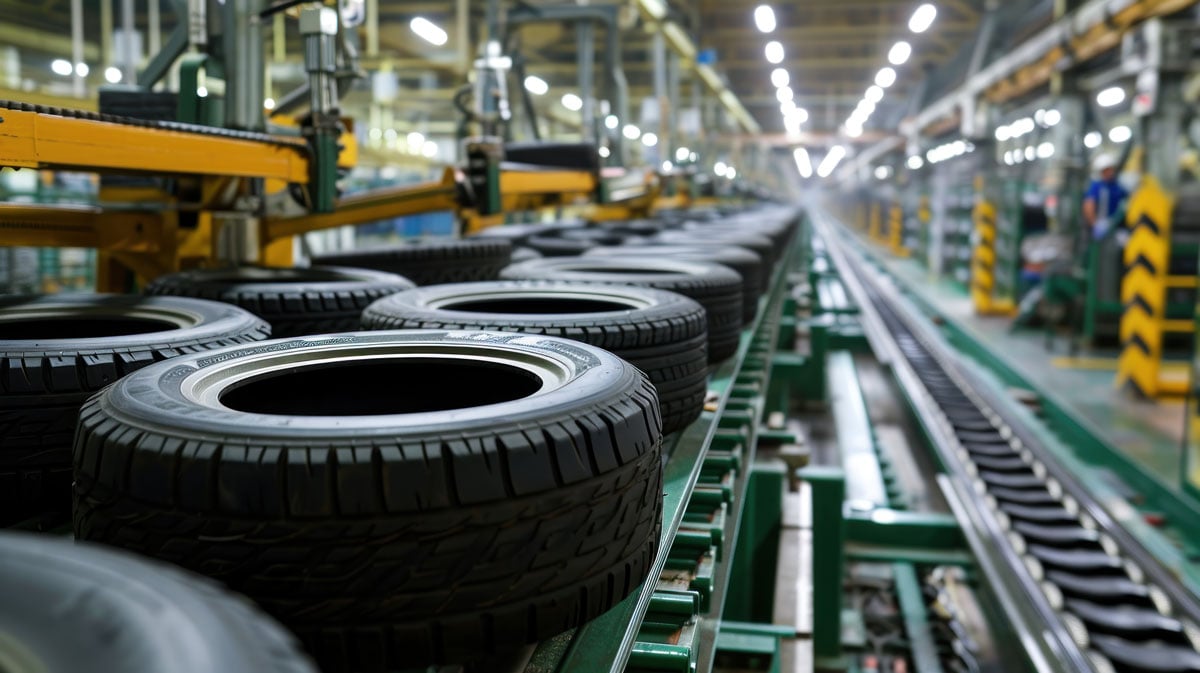
Automotive Parts Manufacturing
Motor
- 415,872 in avoided production losses
- 96 hours of unplanned downtime eliminated
- Increased equipment reliability through early, targeted intervention
A global tire manufacturer partnered with Waites to deploy continuous, AI-powered condition monitoring across key assets, including motors, pumps, and gearboxes.
Waites AI detected an abnormal vibration signature on a drive-end motor bearing. The alert was automatically flagged by the system’s real-time monitoring platform, enabling immediate investigation before the issue escalated into a full-blown failure.
Waites analysts reviewed the AI-generated alert and confirmed a steady increase in high-frequency vibration levels—a known early indicator of bearing degradation. The anomaly aligned with a non-synchronous frequency pattern and axial vibration, further validating the presence of a developing defect.
Without intervention, the motor was at risk of catastrophic bearing failure, leading to significant unplanned downtime and repair costs.
The facility’s maintenance team replaced the defective bearing, opting for a steel cage replacement due to availability constraints. Following the replacement, Waites reinstalled and calibrated the sensor, and post-maintenance analysis confirmed vibration levels returned to normal. Waites continues to monitor the equipment closely to assess performance and ensure the replacement was effective.
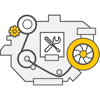
Waites’ monitoring system surfaced the anomaly well in advance of failure, giving the maintenance team time to plan an efficient, non-disruptive response.
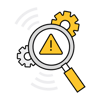
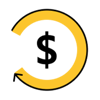
The bearing replacement prevented equipment failure and production downtime, resulting in a cost savings of $415,872.