Is Condition Monitoring Right for Your Facility?
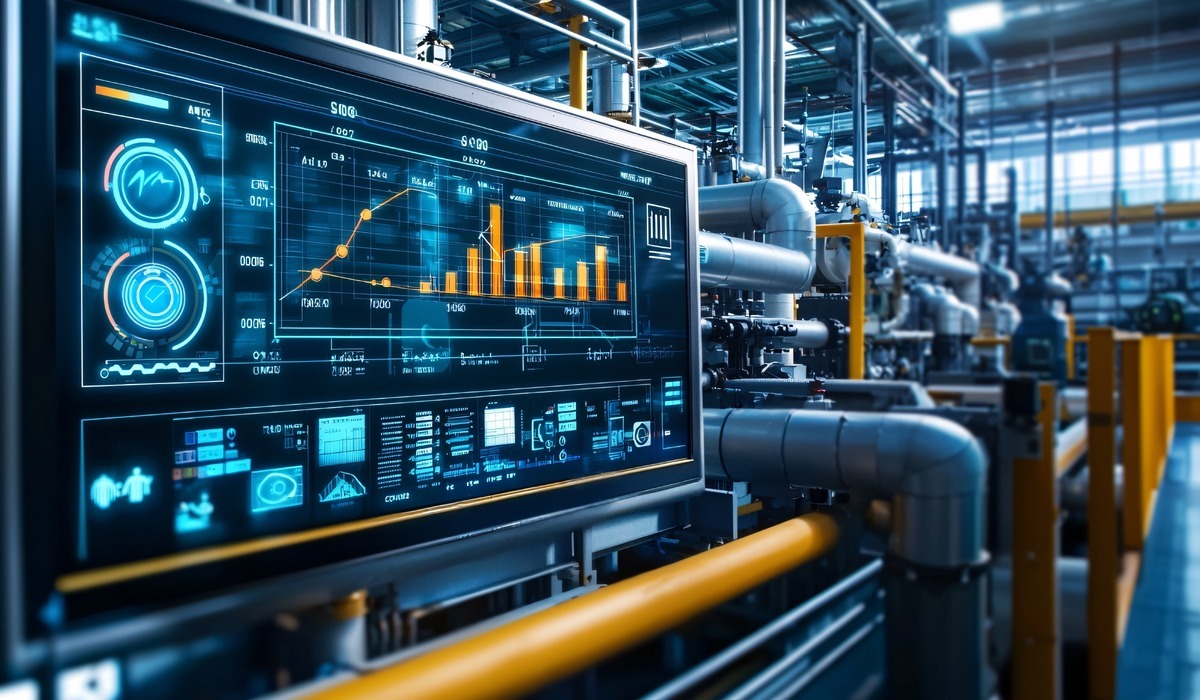
If you're in charge of keeping a facility running, you know the drill: machines break down at the worst possible times. You’re constantly pulled in a dozen directions. You’re short on staff, long on priorities, and still stuck in a cycle of breakdowns and emergency fixes, putting out fires instead of planning ahead.
Sound familiar?
You're not alone. Across industries, teams are battling:
- Aging equipment with no clear signs before failure
- Work orders piling up while technician headcount shrinks
- Pressure to cut costs and increase uptime, all without better tools
Reactive maintenance may have worked a decade ago, but in today’s high-stakes environment, it’s no longer enough. The status quo leads to over-servicing some assets, neglecting others, and getting blindsided by breakdowns that should’ve been preventable.
At Waites, we see this every day: teams doing their best with limited visibility, stuck reacting instead of leading.
Condition monitoring changes that.
Instead of waiting for failure, it gives you the visibility to act ahead of it by tracking vibration, temperature, and other critical data in real time so your team can prioritize what matters and skip what doesn’t.
Knowing when to adopt new technology is just as important as knowing how. This blog will help you assess whether your facility is at a tipping point for condition monitoring, and how to take action when the time is right.
What Is Condition Monitoring, Really?
Condition monitoring is the continuous or periodic tracking of asset health using sensors, software, and analytics. Instead of relying on guesswork or calendar-based schedules, it gives you real-time insights into how your equipment is actually performing so you can take action before a problem leads to downtime.
At its core, a condition monitoring system captures key performance indicators like:
- Vibration patterns that indicate misalignment, imbalance, or bearing wear
- Temperature spikes that signal overheating or friction
- Humidity levels that can affect sensitive components
- Energy usage trends that reveal inefficiencies or abnormal loads
These data points are collected via wireless sensors and sent to a centralized dashboard where they’re analyzed and visualized. From there, your team receives alerts and actionable insights. From there, maintenance teams can take informed action, not just log alerts
The Advantages of Condition Monitoring
-
Spot issues early: Detect problems like abnormal vibration or heat before they escalate into failures
-
Prioritize smarter: Schedule maintenance based on actual condition, not guesses or arbitrary intervals
-
Extend asset life: Reduce over-servicing and wear-and-tear from unnecessary checks or shutdowns
-
Avoid production surprises: Reduce overtime, emergency repairs, and unplanned stops
- Support safety and compliance: Proactively catch risks before they become incidents
- Lay the groundwork for predictive maintenance: Get better insights now and scale later
Is Your Facility Ready? 10 Signs It’s Time for Condition Monitoring
Condition monitoring gives you the tools to shift from reactive chaos to proactive control. If any of these signs sound familiar, it might be time to make the switch.
- Unplanned downtime is disrupting your operation.
Unexpected equipment failures are eating into production time, frustrating your team, and inflating your maintenance budget. Condition monitoring detects problems earlier—reducing costly surprises and making it easier to plan interventions efficiently. - You’re spending too much on emergency repairs and overtime.
Scrambling to find parts, paying for rush shipping, and calling in techs after hours add up fast. With condition monitoring, maintenance becomes more predictable, cutting down on emergency labor and last-minute spending. - Your most critical equipment is too valuable to risk.
If you rely on specialized or high-cost machines to meet production goals, you can’t afford to be in the dark about their condition. Monitoring delivers real-time visibility to protect those assets and extend their lifespan. - Safety or compliance failures could have serious consequences.
In regulated industries or safety-critical environments, unexpected failures can mean much more than downtime—they can trigger injuries, audits, or shutdowns. Early alerts from a monitoring system help you act before risk turns into reality. - Your maintenance team is stretched thin.
With fewer technicians and more assets to manage, your team can’t afford to spend time chasing problems manually. Condition monitoring helps automate oversight, so your team can focus on solving the right problems faster. - You’re managing multiple sites with little visibility.
Whether you oversee two locations or twenty, flying blind is a recipe for inconsistent performance. Condition monitoring gives you a centralized, real-time view of asset health across all facilities so no site is left behind. - You lack real-time data to make confident decisions.
Gut instincts and spreadsheets only go so far. Without hard data, it’s hard to prioritize or justify resource allocation. Monitoring systems give you the insights you need to take control of your maintenance strategy. - Your current strategy is mostly reactive or time-based.
If you’re still relying on calendar-based PMs or fixing things when they break, you’re likely over-servicing some assets and under-protecting others. Condition monitoring lets you align service intervals with actual asset health. - You’re under pressure to improve uptime and performance.
When leadership is looking for leaner operations and higher throughput, reactive maintenance won’t cut it. A monitoring system helps reduce downtime, improve reliability, and support measurable performance gains. - You’re ready for predictive maintenance, but don’t know where to start.
You’ve heard about predictive maintenance. You want to get there, but building a full program from scratch feels overwhelming. Condition monitoring is the natural first step since it’s easy to implement, fast to deliver ROI, and fully scalable.
A Condition Monitoring System That Scales With You
The Waites condition monitoring system is built for real-world industrial environments. Our compact wireless sensors are easy to deploy, even in hard-to-reach areas, and they operate independently from your facility’s wifi so there’s no need for IT involvement.
Beyond hardware, you get 24/7 support from expert reliability analysts who guide your team through diagnosis and resolution, not just deliver alerts.
Waites integrates seamlessly with your existing CMMS, ERP, or asset management systems, so condition data flows directly into your current workflows.
With installations averaging over 1,500 sensors, far above the industry norm, Waites delivers scalable coverage without added complexity.
Unlike many systems that require dedicated headcount or steep learning curves, Waites is designed to work with the team you already have. It's easy to deploy, simple to maintain, and built to reduce—not increase—your staffing and resource demands.
Your Next Step Toward Predictive Maintenance
So, is condition monitoring right for your facility?
If you're battling unplanned downtime, reactive repairs, or limited visibility into asset health, the answer is yes. Condition monitoring gives you the real-time insight and control you need to move beyond reactive maintenance and toward a smarter, more strategic operation.
Waites makes it easy to take that first step. Our wireless sensors are fast to deploy, our platform integrates with the systems you already use, and our expert analysts help you turn data into action, often within days.
Most customers see full ROI in just 3 to 6 months.
Explore how Waites makes condition monitoring simple, powerful, and built for your team.