Achieving Digital Transformation Through Predictive Maintenance
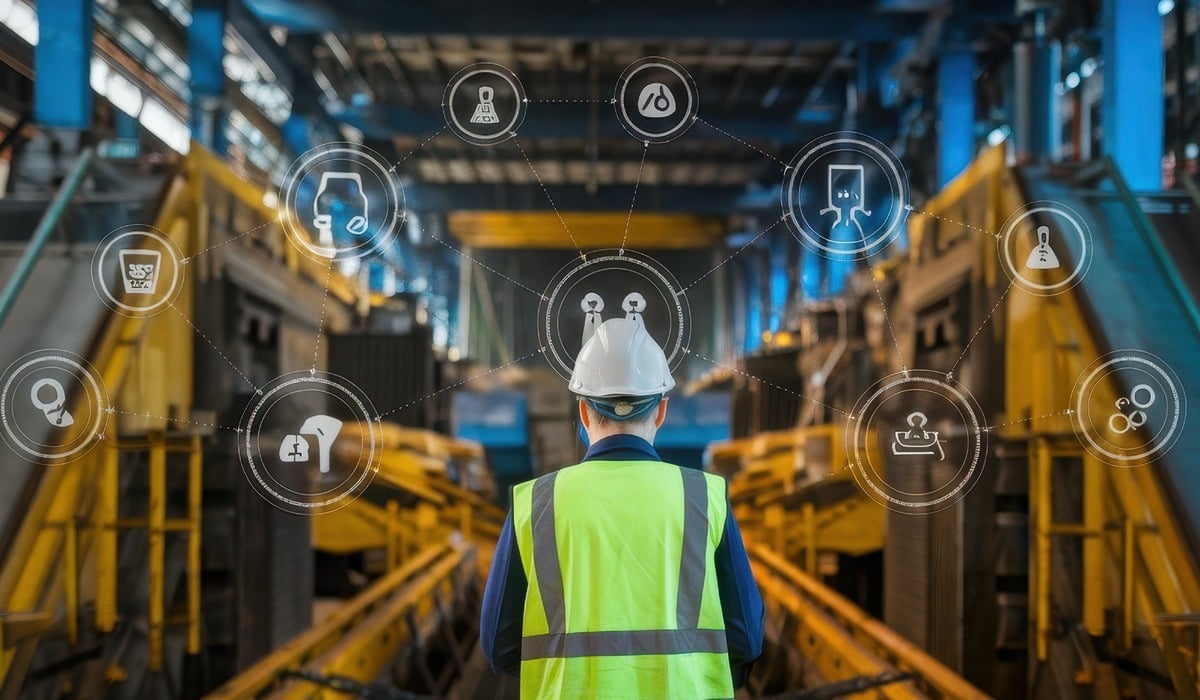
In a world where digital transformation is no longer a luxury but a competitive necessity, industrial organizations are turning to predictive maintenance as a strategic lever for modernization. At the intersection of operational technology (OT) and information technology (IT), predictive maintenance (PdM) enables data-driven decision-making, reduces unplanned downtime, and transforms the traditional maintenance function into a catalyst for enterprise-wide efficiency.
This blog explores how predictive maintenance plays a critical role in digital transformation, offering measurable ROI and unlocking new levels of performance across industries.
What is Digital Transformation in Maintenance?
Digital transformation refers to the integration of digital technologies into every aspect of business operations. In the context of maintenance, it means shifting from manual, reactive workflows to automated, predictive, and data-informed strategies.
Traditional maintenance methods such as reactive (run-to-failure) and preventive (time-based) approaches often result in:
- Unnecessary part replacements
- Missed early warning signs of failure
- High labor and inventory costs
Predictive maintenance changes this by using real-time condition monitoring data and machine learning to detect anomalies before failure occurs. It transforms maintenance from a cost center to a strategic advantage, supporting both operational continuity and enterprise-wide innovation.
How Predictive Maintenance Enables Transformation
1. From Reactive to Proactive
Predictive maintenance uses sensor data and analytics to predict failures. Instead of responding to breakdowns, teams proactively schedule interventions based on asset health, reducing unexpected disruptions and increasing uptime. This shift builds a foundation for reliability and ensures that maintenance aligns with broader performance goals.
2. Integration of OT and IT Systems
Predictive maintenance solutions bridge operational systems such as programmable logic controllers (PLCs) and supervisory control and data acquisition (SCADA) with enterprise software platforms like computerized maintenance management systems (CMMS) and enterprise resource planning (ERP). This integration ensures that maintenance actions are aligned with broader business goals and production schedules. The result is improved coordination between departments, enhanced decision-making, and reduced communication silos.
3. Data-Driven Decision Making
Predictive maintenance brings intelligence to the shop floor. Asset data is collected, analyzed, and visualized in dashboards, empowering leaders to:
- Prioritize work based on risk and criticality
- Justify capital investments using evidence-based insights
- Optimize staffing, training, and inventory planning
Over time, organizations can use this data to benchmark performance, refine KPIs, and support strategic initiatives like sustainability or energy efficiency.
4. Remote Monitoring and Workforce Efficiency
Cloud-based predictive maintenance platforms and mobile apps allow maintenance teams to monitor assets across multiple sites in real-time. This capability is essential in environments facing skilled labor shortages or geographic dispersion. Maintenance leaders can prioritize issues remotely, assign tasks more efficiently, and track resolution in real-time, improving service levels across the board.
5. Standardization Across Sites
For organizations with multiple facilities, predictive maintenance helps unify maintenance strategies. Common metrics and centralized data ensure consistency in performance measurement and resource allocation. Standardization also simplifies training, procurement, and compliance efforts, making it easier to scale best practices across the enterprise.
The ROI of Predictive Maintenance
Organizations pursuing digital transformation often face scrutiny over the return on new technology investments. Predictive maintenance offers a compelling value proposition by delivering quantifiable improvements in cost, efficiency, and asset performance.
Direct Cost Reduction
- Predictive maintenance can deliver a 30 to 50 percent reduction in maintenance costs by eliminating unnecessary preventive tasks.
- Emergency labor and replacement part costs are reduced significantly as breakdowns decrease by up to 70 percent.
Higher Asset Performance
- Predictive maintenance enables equipment life extension by 20 to 40 percent, which delays capital expenditures and improves return on assets.
- Uptime increases, resulting in more predictable and efficient production cycles.
Labor Optimization
- Maintenance planning becomes more effective, reducing overtime and reactive task assignments.
- Resources can be allocated based on risk and condition data, allowing smaller teams to manage larger asset bases without compromising performance.
Strategic Capital Planning
- Asset condition data provides long-term insights into wear patterns, usage trends, and risk profiles.
- Organizations can make smarter investment decisions by prioritizing replacement or upgrades only when justified by performance data.
Increased Safety
- Proactive detection of equipment issues protects personnel and production by minimizing emergency interventions and hazardous breakdowns.
- Safer operations lead to measurable ROI through fewer incidents, lower insurance premiums, and reduced production losses.
Additionally, companies that embrace predictive maintenance often see secondary benefits in areas such as compliance, safety, and energy management. These gains contribute to enterprise-wide improvements and strengthen the case for digital investment.
Getting Started: Steps Toward a Digital Maintenance Future
Here is a strategic roadmap to begin your transformation:
- Identify your critical assets where unplanned failure has major cost, safety, or production implications.
- Select a predictive maintenance platform built for scale with advanced analytics, intuitive dashboards, and support from experienced analysts.
- Install sensors to monitor real-time vibration, temperature, and other performance indicators.
- Integrate with existing systems such as your CMMS, ERP, or asset management software to streamline workflows, automate alerts, and ensure a single source of truth.
- Start with a pilot program on high-impact equipment and expand once early success is documented.
- Train your maintenance and reliability teams on interpreting data, responding to insights, and leveraging the system fully.
- Define success metrics such as downtime reduction, cost savings, and ROI, and review them regularly to guide future investment.
While every organization will follow a slightly different path, these steps offer a practical foundation for embedding predictive maintenance into a broader digital strategy.
Predictive Maintenance as a Cornerstone of Industry 4.0
Predictive maintenance is more than a technical upgrade. It represents a mindset shift toward strategic asset management, continuous improvement, and operational resilience. As industries embrace automation, data science, and intelligent systems, predictive maintenance stands out as a practical and low-barrier, high-impact starting point.
By leveraging real-time data and machine learning, organizations can prevent failures, reduce costs, and maximize asset value. More importantly, predictive maintenance positions maintenance and operations teams as critical drivers of digital transformation, unlocking value far beyond the plant floor.
Whether your organization is just beginning its digital journey or looking to optimize existing initiatives, investing in predictive maintenance is an essential step toward achieving long-term success in an increasingly competitive industrial landscape.
Explore how Waites helps industrial teams modernize maintenance.