The Cost of Equipment Failures: 10 Common Issues and How to Solve Them
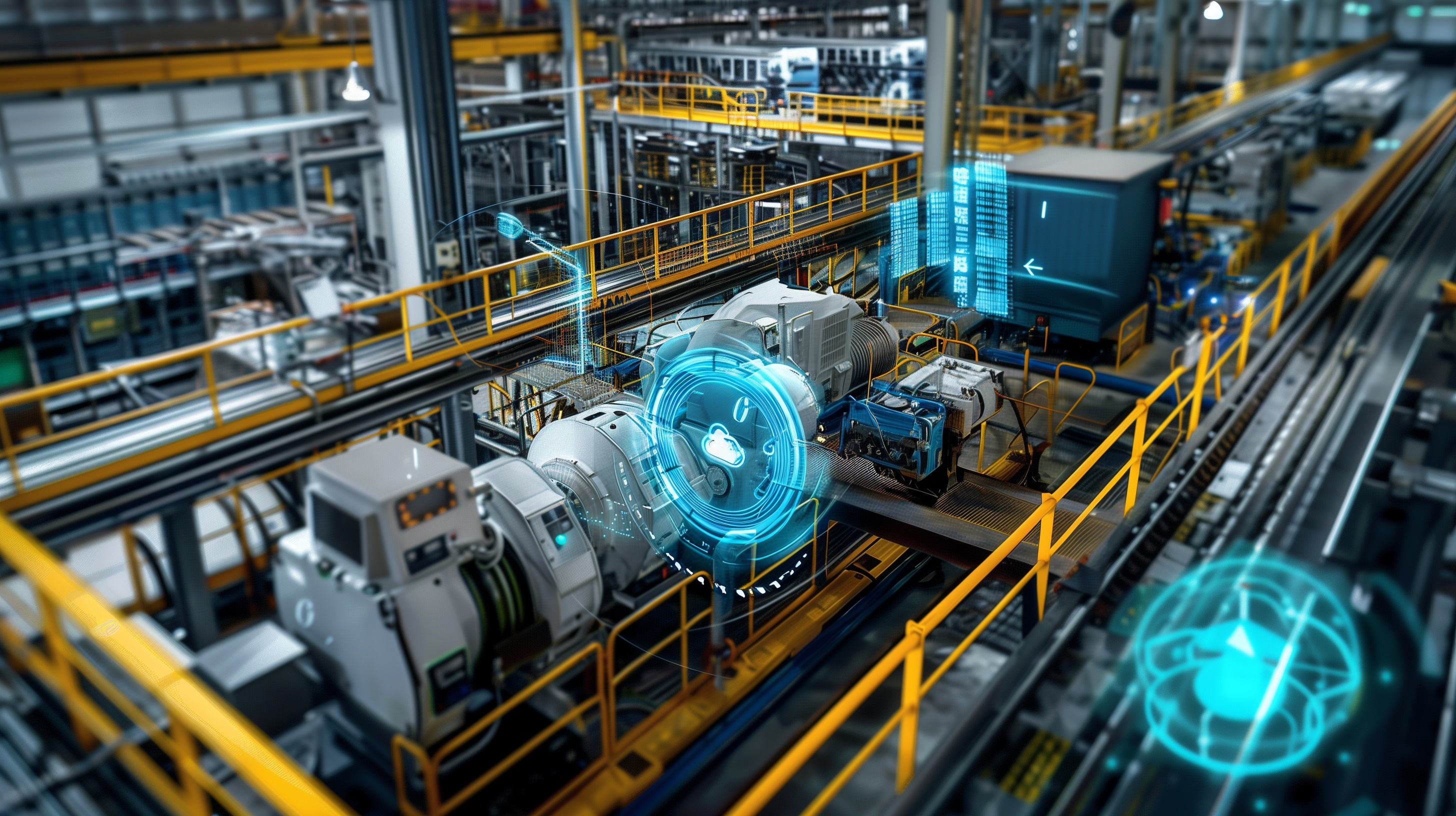
In today’s high-pressure manufacturing environments, downtime isn’t just inconvenient—it’s expensive. In fact, unplanned downtime costs industrial manufacturers an estimated $50 billion annually. And while that number is staggering, what’s more shocking is this: the majority of equipment failures are entirely preventable.
The truth is, machines rarely fail without warning—they vibrate, overheat, and behave differently long before they break down. But unless you're constantly monitoring them, those warning signs go unnoticed. That's where remote condition monitoring comes in and where Waites’ predictive maintenance solution makes all the difference.
Waites provides continuous temperature and vibration monitoring that helps you spot early signs of trouble long before failure strikes. This blog explores the 10 most common machine failures in manufacturing and explains how Waites helps detect and prevent them with smart, real-time condition monitoring.
10 Common Equipment Failures and How to Prevent Them
1. Unbalance
What It Is:
Unbalance happens when the mass distribution in a rotating component—like a fan, rotor, or impeller—is uneven, causing the machine to wobble during operation.
Why It’s Costly:
Unbalance leads to excessive vibration, accelerated bearing wear, structural fatigue, and even catastrophic failure if left unaddressed.
Early Warning Signs:
- High vibration amplitude at 1X the running speed
- Audible noise and visual wobble
- Increased wear on bearings and seals
How Waites Helps:
Waites vibration sensors detect unbalance by analyzing FFT data and identifying a strong peak at 1X frequency. Powered by AI-driven analysis and continuous monitoring, Waites alerts your team the moment vibration levels exceed acceptable thresholds so you can balance components before they cause downstream damage.
2. Coupling Misalignment
What It Is:
Coupling misalignment occurs when the shafts of two connected machines (e.g., motor and pump) are not aligned correctly, either angularly or in parallel.
Why It’s Costly:
Misalignment puts excessive stress on bearings, couplings, and seals, leading to overheating, fatigue, and shortened machine lifespan.
Early Warning Signs:
- Elevated vibration at 1X, 2X, and 3X running speeds
- Shaft wear and premature bearing failure
- Heat buildup at coupling joints
How Waites Helps:
Waites enables phase analysis with multi-sensor data collection, making it easy to distinguish angular from parallel misalignment. Your maintenance team gets clear vibration patterns and real-time alerts tied to misalignment signatures, enabling early correction and extended asset life.
3. Bent Shaft
What It Is:
A bent shaft is a physical deformation in a rotating shaft, often caused by improper handling, manufacturing defects, or overload conditions.
Why It’s Costly:
Even minor bends cause instability in rotation, misalignment, and intense stress on connected components, accelerating overall degradation.
Early Warning Signs:
- Non-sinusoidal vibration waveform
- Consistent radial/axial vibration anomalies
- Difficulty aligning couplings
How Waites Helps:
With Waites, you get detailed waveform data and harmonic analysis that clearly show the presence of shaft deformation. Ongoing data trending lets you see progressive changes and pinpoint the moment when action is needed before damage spreads.
4. Resonance
What It Is:
Resonance occurs when the natural frequency of a machine or component aligns with an excitation frequency, leading to amplified oscillations.
Why It’s Costly:
Undetected resonance can lead to cracks, fastener failure, and even structural collapse due to prolonged vibration amplification.
Early Warning Signs:
- Sharp spikes in vibration at certain speeds
- Excessive movement without a clear mechanical fault
- Vibrations increasing dramatically with speed changes
How Waites Helps:
Waites makes resonance detection simple by enabling controlled frequency sweeps and monitoring how vibration amplitudes respond. Its high-resolution FFT analysis pinpoints natural resonant frequencies so you can adjust operating ranges or stiffen structures to avoid destructive harmonics.
5. Bearing Failure
What It Is:
Bearings support rotating elements, and failure occurs when rolling elements or races degrade due to contamination, overload, or fatigue.
Why It’s Costly:
A failed bearing can seize shafts, destroy housings, and halt entire production lines—often with minimal warning.
Early Warning Signs:
- High-frequency vibration (bearing fault frequencies: BPFO, BPFI, BSF, FTF)
- Audible grinding or whirring
- Temperature increases near bearing housings
How Waites Helps:
Waites features a built-in bearing fault frequency library that detects and tracks characteristic vibration patterns associated with inner race, outer race, ball, and cage defects. Our system alerts you to early-stage anomalies—often well before audible noise or heat is present—so you can schedule proactive bearing replacements and avoid unexpected downtime.
6. Mechanical Looseness
What It Is:
Looseness happens when components such as bolts, mounts, or couplings are no longer tight, often due to wear, vibration, or poor installation.
Why It’s Costly:
Left unchecked, looseness causes impact damage, accelerates fatigue, and increases the risk of catastrophic machine failure.
Early Warning Signs:
- Broad-spectrum vibration with high harmonics (1X, 2X, 3X…)
- Clanging or rattling sounds during operation
- Unstable or shifting components
How Waites Helps:
Waites sensors detect signature harmonic patterns and transient impacts associated with looseness. Our platform’s trend analysis flags increasing instability over time, empowering your team to tighten secure components or reinforce mounting structures before failure occurs looseness leads to failure.
7. Gear Failure
What It Is:
Gear failure happens when gear teeth become worn, misaligned, cracked, or pitted due to poor lubrication, fatigue, or excessive load.
Why It’s Costly:
Gears drive critical systems. Failures can stop conveyors, mixers, or reducers, resulting in sudden and costly downtime.
Early Warning Signs:
- Noise: whining, clicking, or grinding
- Vibration peaks at gear mesh frequency (GMF) and sidebands
- Increased torque resistance or slippage
How Waites Helps:
Waites provides automatic detection of gear mesh frequency (GMF) and associated sidebands using gear fault libraries. You can visualize progressive wear and receive automatic alerts when gear health begins to degrade long before mechanical issues become visible or cause downtime.
8. Electrical Faults
What It Is:
Electrical faults in motors include issues like winding shorts, phase imbalance, rotor defects, and poor insulation.
Why It’s Costly:
Undetected faults can reduce efficiency, overheat systems, and result in full motor burnout.
Early Warning Signs:
- Increased vibration at 2X line frequency (e.g., 120 Hz in North America)
- Electrical current anomalies
- Irregular motor startup behavior
How Waites Helps:
Waites detects electrical-related vibration frequencies—such as sidebands around line frequency—that often appear even when mechanical systems seem healthy. even when mechanical systems seem fine. By correlating this data with current draw (via integrated monitoring), Waites helps uncover issues like rotor bar defects or phase imbalance without the need to open the motor.
9. Electromagnetic Interference (EMI)
What It Is:
EMI is electrical noise from nearby equipment (like VFDs or welders) that interferes with vibration sensors or communications.
Why It’s Costly:
EMI can mask real issues or generate false positives, leading to incorrect decisions and unnecessary service calls.
Early Warning Signs:
- Spurious vibration peaks not related to machine harmonics
- Intermittent or erratic sensor signals
- Sudden noise in wireless communication
How Waites Helps:
Waites sensors are EMI-hardened and backed by robust signal filtering to ensure clean, trustworthy data. The system compares readings across multiple axes and locations to distinguish real faults from EMI artifacts so you can act on your data with confidence.
10. Thermal Overload
What It Is:
Thermal overload occurs when machines exceed their optimal operating temperature due to overuse, friction, poor ventilation, or electrical resistance.
Why It’s Costly:
Overheating causes lubricant breakdown, component distortion, and eventually machine seizure or fire risk.
Early Warning Signs:
- Gradual rise in surface or housing temperatures
- Increased vibration from thermal expansion
- Reduced efficiency or speed
How Waites Helps:
Waites combines vibration and temperature sensing in one platform. As temperature rises, Waites correlates heat trends with vibration signals, revealing root causes like friction, misalignment, or bearing distress. The result? Actionable alerts before thermal stress becomes irreversible damage.
Protect Your Assets with Predictive Maintenance
Unplanned downtime costs manufacturers millions each year often because of issues that could have been caught early. From bearing failures to misalignment, bent shafts to overheating, the warning signs are there. The problem isn’t a lack of data—it’s a lack of visibility at the right time.
With Waites, you gain that visibility. Our wireless, scalable condition monitoring system helps detect all 10 of the most common (and costly) machine failures before they cause breakdowns. That means fewer surprises, safer operations, and more control over your equipment’s performance.
The stakes are high, but so is the potential for savings. Don’t wait until something breaks. Start catching failures before they happen.